|
|
LA COSTRUZIONE
GUINNES WORLD RECORD : "URCA
FOR RECORD" |
|
|
|
|
Disegni e master in legno ed espanso |
|
Per
abbattere i costi e i tempi di realizzazione, lo stampo è
stato realizzato in espanso e legno, scomponibile sul piano
longitudinale in 2 metà.
Tutta la costruzione e i piazzamenti sono realizzati
mediante spinature e tracciature sul piano di taglio che
diventa piano di riferimento.
Qui si vedono le ordinate longitudinali e la chiglia in fase
di preparazione : si ritagliano le copie dei disegni in
scala 1:1 e si incollano direttamente sul legno.
Ogni parte viene tracciata e ritagliata separatamente prima
dell’assemblaggio curando in particolare le simmetrie e il
rispetto delle quote di progetto. |
|
|
|
|
Dopo la
spinatura delle due centine longitudinali tra loro, e con il
piano di montaggio, si procede all’assemblaggio con la chiglia
superiore ed inferiore.
Le parti vengono imbastite e messe in squadra sul piano di
costruzione mediante spilli e puntatura con cianoacrilato.
Completato l’assemblaggio delle ordinate/chiglie, l’insieme
viene rispinato e raccordato per ottenere una perfetta
giunzione delle parti in legno che faranno da struttura
portante del master in espanso.
Le ordinate, completata la laminazione, verranno poi staccate
dal master e formeranno la nervatura di giunzione tra i due
"mezzi scafi".
Quindi si procede a piazzare
le centine in depron da 6mm e i riempimenti in styrodur ad
alta densità. In tal modo si genera una forma maggiorata dello
scafo da sagomare in un secondo tempo. |
|
|
|
|
Preparazione master
per laminazione |
|
Mediante
sgrossatura con taglierino e lisciatura con tampone e carta
abrasiva in poche decine di ore si arriva ala forma finale
pronta per la laminazione.
Sul piano di
lavoro protetto da nylon si procede a rivestire con
pellicola trasparente per alimenti i due semiscafi
ottenendo una superficie liscia e perfettamente "distaccante"
tra master e parti da laminare. |
Bloccata la
pellicola plastica con nastro adesivo al di fuori della zona
da laminare, si procede alla tensionatura mediante phon ad
aria calda industriale per eliminare tutte le grinze e
farle copiare perfettamente la forma del master.
Completata la tensionatura si controlla la superficie a
luce radente per individuare eventuali difetti che, se non
eliminati, si trasferiranno al laminato. |
|
|
|
|
Laminazione e
postcura delle parti in fibra di carbonio |
|
Ora si
possono tagliare tutte le pezze di tessuto che
andranno impregnate di resina epossidica e poi si può
iniziare la loro stesura. All’interno dello scafo viene
posto uno strato di tessuto di vetro fine, poi gli strati di
tessuto di carbonio impregnandoli con resina epossidica
Cyba: tutti i materiali sono forniti dallo sponsor
Modelresine. |
|
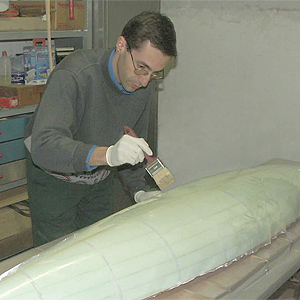 |
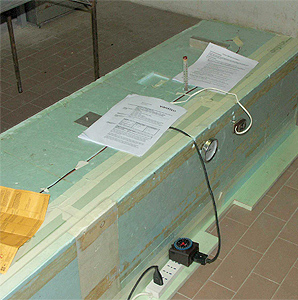 |
|
Infine si
lamina lo strato di vetro di finitura esterna. Date le
dimensioni la presenza di alcuni “supporter” è un grande
aiuto. Anche la resina va preparata un poco alla volta per
lavorarla con la giusta viscosità. Dalle immagini si vede la
parte superiore dello scafo completamente laminata in fase
di polimerizzazione.
Il tempo totale impiegato è stato di circa 6 ore in 2-3
persone.
Completa la
polimerizzazione a temperatura ambiente (24-48ore) è
stata effettuata la postcura a 60 gradi delle parti
in composito per far raggiungere al laminato le massime
caratteristiche meccaniche.
E' stato realizzato per questo scopo un forno "su misura"
con un sistema termostatico temporizzato di controllo per
rispettare i parametri di postcura previsti dal produttore
della resina (Cyba Renlam 5138).
Completato il ciclo di postcura le parti vengono rimosse dal
forno, rifinite e controllate. |
|
|
|
|
|
Laminazione deriva in
fibra di carbonio |
|
Con una
tecnica simile, ma utilizzando anche un sacco a vuoto per una
maggiore compattazione del composito è stata realizzata la
deriva che, con soli 11mm di spessore e 700 grammi di peso,
porta fino a 12Kg di zavorra appesi ad un metro sotto alla
coperta. |
|
|
|
|
Preassemblaggio e
prove in “vasca” |
|
Data una mano
di vernice di fondo, i due "semi-scafi" in carbonio (1490
grammi di peso complessivo) sono pre-assemblati e tracciati
per la loro prima prova in acqua di verifica della esattezza
dei calcoli di progetto. Vengono infatti tracciati i
riferimenti della linea di galleggiamento, il centro di
rotazione e il posizionamento dei vari pesi esterni ed
interni.
Finalmente lo
scafo può essere messo in acqua con le varie masse simulanti
la zavorra, l’albero, l’impianto radio, i verricelli, etc.
Tutto viene posto nelle posizioni previste a progetto con la
massima precisione: è il momento più importante della
verifica!
Ed eccola che
galleggia esattamente come previsto dai calcoli per 16,5 Kg di
dislocamento. Adesso si può procedere nella costruzione
seguendo i disegni e le assunzioni di base. Il sistema di
calcolo è perfettamente a punto! |
|
|
|
|
Laminazione rinforzi
interni coperta |
|
Nello scafo
superiore vengono laminati i rinforzi e incollati punti di
attacco delle strutture di coperta e dei boccaporti. |
|
|
|
|
Assemblaggio e
incollaggio delle parti su ordinata intermedia |
|
Le due parti
dello scafo vengono più volte pre-assemblate per verificare le
interfacce e i punti di attacco. Ogni particolare deve essere
previsto con esattezza prima della chiusura dei due "gusci":
nulla può essere lasciato "al caso", molte zone dello scafo
dopo non saranno più raggiungibili.
L’assemblaggio finale prosegue montando l’ordinata centrale
sullo scafo “inferiore” e piazzando la scassa della deriva,
quella dell’albero e i punti di attacco del sartiame.
Si procede
quindi all’incollaggio dell’ordinata centrale sul guscio
inferiore. Dopo di che si incollano in posizione: la scassa
della deriva e quella dell’albero, gli attacchi delle sartie,
del timone, della piastra radio e tutti i rinforzi
sottocoperta. |
|
|
|
|
|
Finiture raccordi
dopo chiusura scafo |
|
Dopo l’unione
dei due semigusci si procede alla stuccatura della giunzione e
dei raccordi tra scafo e deriva. Utilizzando resina epossidica
caricata con fibre di carbonio e microsfere si ottiene la
massima robustezza e una buona uniformità di durezza tra gli
riempimenti e le zone in CFC laminate.
Tra le parti smontabili, come distaccante, viene interposta la
solita pellicola trasparente per alimenti. |
|
|
|
|
Verniciatura scafo
|
|
Dopo lunga
levigatura e raccordatura si giunge finalmente alla
verniciatura |
|
|
|
|
Montaggio
attrezzature di coperta |
|
Non rimane che montare le attrezzature
nelle posizioni previste sui rinforzi annegati e filettati
sottocoperta.
Rinvii, cavallotti, meccaniche di albero e boma: poco alla
volta l’attrezzatura prende forma. Ogni particolare è
essenziale per evitare ogni possibile sporgenza su cui le
manovre potrebbero impigliarsi.
Massima cura è posta alle superfici che sono tutte
raccordate e concepite per la massima leggerezza: la
meccanica completa di albero, bomi e coperta pesa in tutto
poco più di 150 grammi. |
In questa vista di dettaglio si notano:
- I due elastici che mantengono in tensione le scotte delle
vele sui verricelli
- Gli attacchi regolabili delle sartie
- Il piede dell’albero con il sistema di tensionatura del
sartiame e le cerniere del boma.
- La meccanica del boma del fiocco che permette di regolare
la tensione della balu-mina, l’angolo di rotazione e “il
grasso” nelle varie andature.
- due cavallotti di sollevamento dello scafo, uno in
posizione baricentrica e uno a prua. |
|
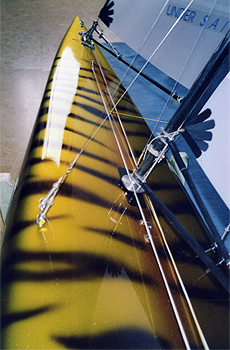 |
|
|